WQARF | WCP North Plume - History
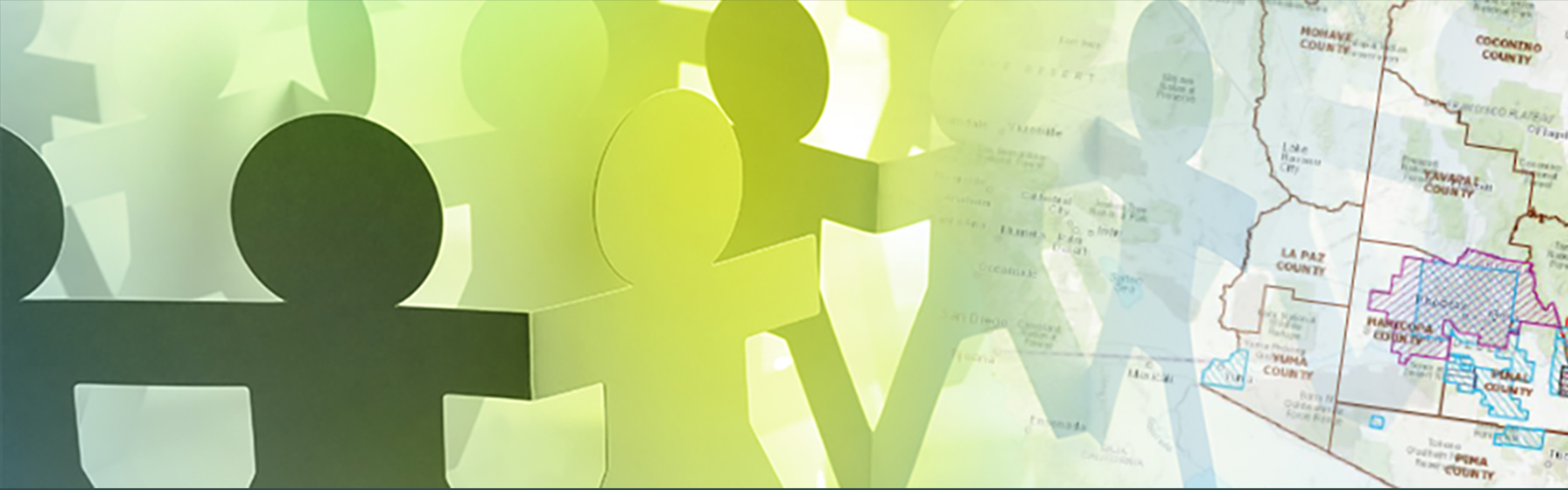
Site History
2024: ADEQ operated the soil vapor extraction (SVE) system on an intermittent schedule and conducted groundwater monitoring activities at the site. Soil vapor rebound monitoring was performed in accordance with the SVE operation schedule.
2023: ADEQ operated the SVE system on an intermittent schedule, continued enhanced reductive dichlorination (ERD) injections, and conducted groundwater monitoring activities at the site. Soil vapor rebound monitoring was performed in accordance with the SVE operation schedule.
2022: ADEQ operated the SVE system, continued ERD injections, and conducted groundwater monitoring activities at the site. The SVE treatment system was shut down in April for a soil vapor rebound evaluation and transition to an intermittent operation schedule.
2021: ADEQ operated the SVE system, implemented an SVE heat injection pilot study, continued ERD injections, and conducted groundwater monitoring activities at the site.
2020: ADEQ operated the SVE system, continued ERD injections, and conducted groundwater monitoring activities at the site. ADEQ also issued the Record of Decision for the site in August.
2018 – 2019: ADEQ operated the SVE system, continued ERD injections, and conducted groundwater monitoring activities at the site.
2017: The Proposed Remedial Action Plan was released in August. The F&B Manufacturing Inc. Facility (F&B) SVE system was operated continually except during minor maintenance activities. ADEQ continued ERD injections at the F&B release area. Groundwater sampling was conducted in the vicinity of the injection wells to track remedial progress.
2016: The SVE system was operated continually except for shutdown for minor maintenance activities. Three injection wells were installed at the F&B Facility and ADEQ initiated an ERD study to isolate zones within the aquifer for treatability. This effort was conducted to accelerate time to cleanup.
2015: The Feasibility Study report was completed. The SVE system was operated continually except for shutdown for minor maintenance activities. Groundwater monitoring and sampling was conducted in February and March.
2014: This SVE system was shut down at the end of December due to high moisture content in the air stream. The system was restarted at the end of March. The SVE system was modified in June to more efficiently remove moisture from the air stream to allow operation of the system year-round. Granular activated carbon was changed out in the three lead canisters in June. Groundwater monitoring and sampling was conducted in March and groundwater elevations were measured in June.
2013: Three new SVE wells were installed and connected to the existing SVE system at F&B. This SVE system was shut down at the end of January due to high moisture content in the air stream. The system was restarted at the end of April. Groundwater monitoring and sampling was conducted in March and September. Groundwater elevations were measured in June and December.
2011 – 2012: The SVE system at F&B was shut down in February because of high moisture content in the air stream. The system was restarted in April.
2010: The SVE system at F&B was shut down during the first quarter of 2010. The system was restarted in April. The SVE system at Hill Brothers Chemical Company (HBCC) was shut down and dismantled. A no further action memo for soils underlying the HBCC facility was issued.
2009: The SVE treatment systems continued to operate to further remove volatile organic compounds (VOCs) from the soil and eliminate the VOCs from becoming potential contaminants in the groundwater in the West Central Phoenix (WCP) area.
2008: Three new wells were installed in the project area. One well was the result of a Prospective Purchaser Agreement with the state of Arizona. In a public benefit arraignment, the new well was installed in the western portion of the project area. Additionally, two wells were installed in an effort to evaluate the potential to capture and treat contaminated groundwater.
HBCC installed an SVE treatment system to be operated to remediate potentially contaminated soils beneath the facility.
2007: As of December, over 41,400 pounds of VOCs were captured by the SVE system at the F&B manufacturing facility. ADEQ had a Groundwater Risk Model performed with information available from the former Rinchem facility. Based upon the results of the model, it was determined that the concentration of VOCs in the soil did not merit the placement of a remedial system.
2006: In August, ADEQ issued the draft RI report. Groundwater samples and water level measurements were collected in September.
2000 – 2006: ADEQ operated an SVE system at the F&B facility since August 2001 to remediate the tetrachloroethylene (PCE) contamination beneath the vapor degreaser. In addition, ADEQ removed approximately 210 cubic yards of soil beneath the vapor degreaser during two excavations in July 2000 and September 2001. As of December 2006, over 41,000 pounds of PCE were removed from the source area by the SVE system.
1995 – 1999: From 1995 until 1998, F&B was financially unable to fulfill the requirement under the consent decree (CD). Between 1998 and 1999, ADEQ and F&B negotiated a new CD, which was approved by the Court in August 1999. As stated under the new CD, ADEQ would complete the RI/FS and conduct the remediation of the facility. In 1999, ADEQ and F&B entered into a financial hardship CD in Federal Court. Under the CD, ADEQ conducts the RI/FS and remediation. F&B was required to make annual payments for a period of time in amounts calculated as a percentage of net sales.
The site was placed on the WQARF Registry in April 1998 with a score of 50 out of a possible 120. The site score was re-evaluated in 2000 with a revised score of 55.
1992: ADEQ entered into a CD with F&B to conduct an RI/FS, remediate PCE-contaminated soil on-site, reimburse past costs and pay oversight costs.
1982 – 1989: VOCs were first detected in groundwater in the WCP area in July 1982. The City of Phoenix (COP) detected trichloroethene (TCE) in four municipal public supply wells, COP Wells #70, #71, #151, and #152. The Arizona Department of Health Services, Salt River Project and the COP confirmed the presence of VOCs in the groundwater with sampling in 1983, 1985, and 1986. Groundwater from COP wells #70 and #71 contained the highest concentrations of TCE and, therefore, were immediately shut down. Wells #151 and #152 were monitored for VOC concentrations from 1982 until 1989. As a result of sampling conducted during February of 1989, COP elected to take both wells #151 and #152 off-line on March 7, 1989.
The former Rinchem Company, Inc. facility was located near 41st Avenue and Turney Avenue. Rinchem operated a chemical warehouse and distribution facility from 1982 through June 1993 that handled solvents, oils, and fuels. Several suspected sources were identified on the Rinchem facility, including the former repackaging area and former tank farm.
Field investigation activities for the site were conducted between 1984 and the present time. Several contaminants have been detected in soil and groundwater samples collected during field investigations at the four facilities. The primary contaminants of concern were TCE, PCE, and 1,1-dichloroethene (1,1-DCE).
Four facilities were identified as likely sources of the groundwater contamination in the site. The four facilities were as follows: the F&B facility, Pyramid Industries, Inc. (Pyramid) facility, former Rinchem facility, and HBCC facility. Field investigation activities at the four facilities in the site have been conducted since 1984.
In 1987, the WCP area was designated a WQARF priority list site.
1977: The former Pyramid facility was also located near 39th Avenue and Montecito Avenue, across from the F&B facility. Pyramid operated a telephone and television cable riser box manufacturing facility from 1977 to 1994. Operations at the facility required the use of acids, caustics, heavy metals, paints, and methylene chloride. Several suspected sources of contamination have been identified on the Pyramid facility, including the loading dock/drywell, paint room, and historic hook cleaner area.
1969: The HBCC, a facility in the North Plume project area, was located near 42nd Avenue and Turney Avenue. The HBCC facility operated as a chemical distribution facility at this location since 1969. Chemicals that included acids, bases, solvents, chlorine, and concrete additives were stored in above ground storage tanks on-site prior to transfer into containers for distribution.
1967 – 1991: The F&B facility was located near 39th Avenue and Montecito Avenue. Since 1967, F&B manufactured metal aircraft and spacecraft parts and performed sheet metal forming, and assembly. Solvents were used as degreasing agents to clean the surface of the metals. PCE was used as the degreasing solvent until approximately October 1987, when it switched to 1,1,1-trichloroethane (TCA). In April 1991, ADEQ discovered information that PCE had leaked from F&B's degreaser into the soil under the building.